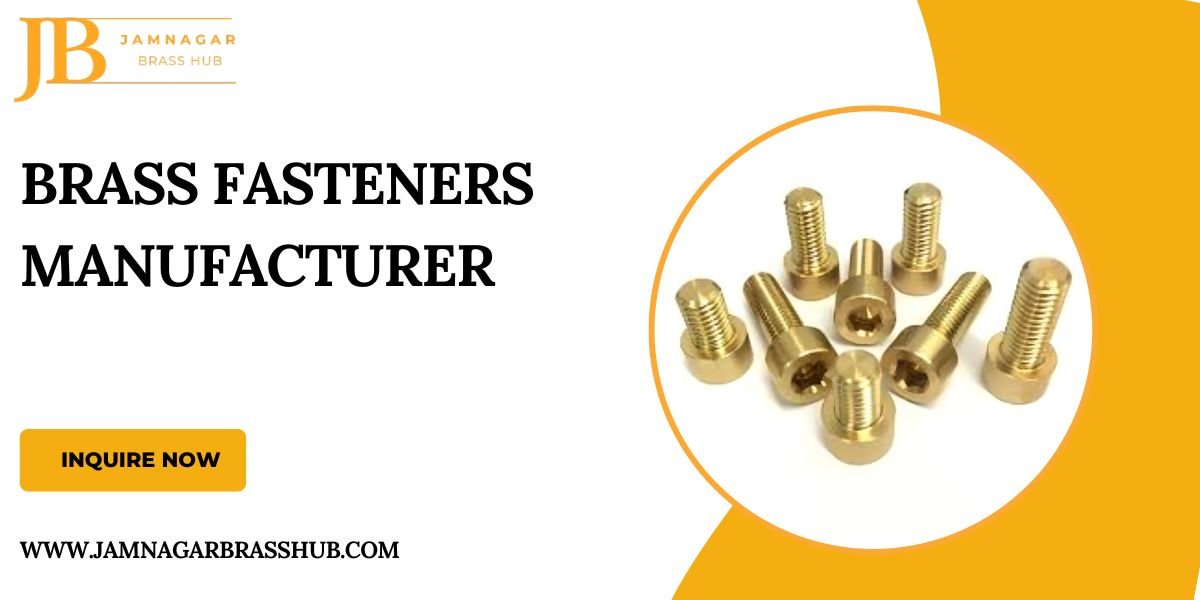
Brass Fasteners Manufacturer
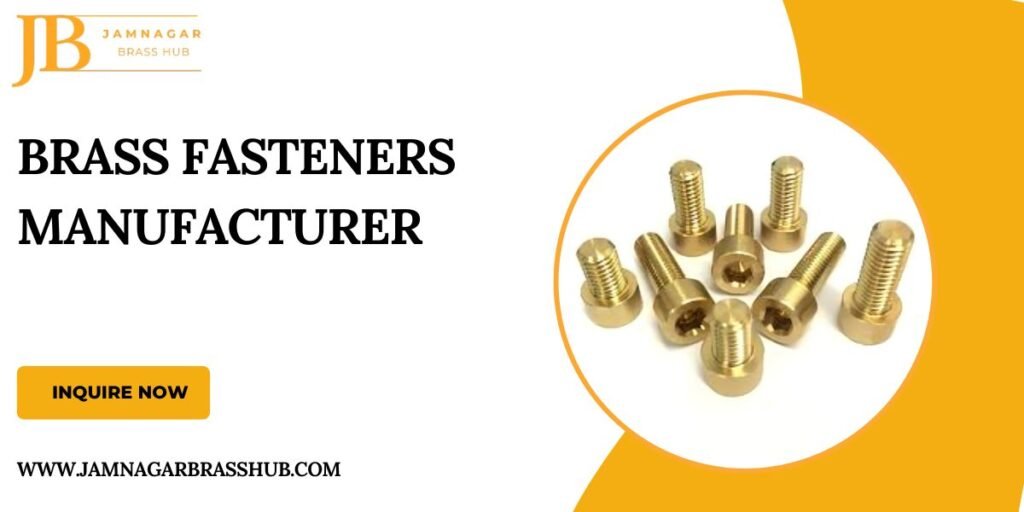
Brass Fasteners Manufacturer | Brass Fasteners Supplier | Brass Fasteners Wholesaler | Best Quality of Brass Fasteners at Best Prices |
Introduction
The desire for lasting and high-performance fasteners in industries such as construction, automotive, electronics, and marine has resulted in a wide range of materials utilized in fastener manufacturing. Brass is a very durable material known for its great qualities such as corrosion resistance, electrical conductivity, and aesthetic appeal. Brass fasteners have become a popular choice in a variety of industries due to their adaptability, durability, and long life. In this detailed article, we will look at the world of brass fasteners, including their types, manufacturing processes, and the role of significant manufacturers in the market, with a specific emphasis on Jamnagar Brass Hub, a pioneer in the brass fasteners sector.
Why Brass Fasteners?
Brass, an alloy of copper and zinc, combines the best features of both metals. Here are the main reasons why brass is commonly utilized in fastener manufacturing:
- Corrosion Resistance: Brass is extremely resistant to corrosion, particularly from water and most acids. This makes it a good alternative for fasteners used in maritime and outdoor environments.
- Brass is a good conductor of electricity, hence brass fasteners are ideal for use in electrical and electronic applications.
- Malleability: Brass is easily molded, cut, and shaped, allowing producers to produce fasteners of varied forms and sizes with precision.
- Aesthetic Appeal: The golden luster of brass lends a pleasing touch to any building or assembly project. This is especially relevant in decorative applications where appearance is critical.
- Durability: Brass fasteners are extremely strong, giving dependability and stability in heavy-duty applications. They are also softer and more malleable than steel, making them easier to work with.
Types of Brass Fasteners
Brass fasteners exist in a variety of shapes, each having a different purpose depending on the application. Some of the most frequent types of brass fasteners are:
- Brass screws are commonly utilized in woodworking, plumbing, and electrical applications. Brass screws are nonmagnetic, rust-resistant, and suitable for both indoor and outdoor applications.
- Brass bolts, known for their strength and corrosion resistance, are utilized in machinery, electrical components, and marine applications where water and corrosion resistance is essential.
- Brass Nuts: Like brass bolts, brass nuts are intended to offer a secure hold in various assemblies. They are frequently utilized in electrical applications due to their non-corrosive properties.
- Brass washers are used to distribute the load of fasteners such as screws and bolts, reducing surface wear and increasing fastener strength.
- Brass Rivets: Rivets are permanent fasteners that link two surfaces. Brass rivets are suitable for decorative purposes and are commonly used in furniture, boats, and other visually demanding applications.
- Brass Studs are threaded fasteners used in the construction, plumbing, and automotive industries to provide secure and long-lasting fastening solutions.
The Manufacturing Process of Brass Fasteners
Brass fasteners are made using a precise and well controlled process that guarantees longevity, consistency, and performance. Here’s a step-by-step look at the manufacturing process.
1. Alloy Preparation
Brass is made by combining copper and zinc in different proportions, depending on the desired properties. For fasteners, the ratio of copper to zinc typically ranges between 60% and 40%, resulting in a durable alloy with high corrosion resistance.
2. Casting
Once the alloy composition is prepared, it is cast into billets or rods. These rods will later be cut down to form the base material for the fasteners.
3. Forging
In the forging process, the brass rods are heated to make them malleable. This allows manufacturers to mold the metal into the desired shapes. In the case of fasteners, the metal is shaped into screws, bolts, or other forms through a process of hammering and compression.
4. Machining
After the initial forging process, the fasteners undergo machining to achieve the desired dimensions and surface finish. Lathes, milling machines, and CNC machines are used to drill holes, cut threads, and ensure precision in the design of each fastener.
5. Surface Treatment
To enhance the appearance and longevity of brass fasteners, they may undergo surface treatments such as polishing, plating, or coating. This step also helps improve the corrosion resistance and aesthetic appeal of the fasteners.
6. Quality Control
Once the fasteners are produced, they are subjected to rigorous quality control tests to ensure that they meet the industry’s highest standards. Tests may include stress testing, corrosion resistance checks, and dimensional accuracy evaluations.
7. Packaging and Distribution
After passing quality control, the fasteners are packaged and prepared for shipment to distributors, retailers, or directly to clients.
Applications of Brass Fasteners
Brass fasteners are employed in a variety of sectors due to their distinctive features. Some of the prominent applications are:
- Maritime Industry
Brass fasteners are favored in the marine industry because they resist corrosion induced by exposure to saltwater and moisture. They are widely utilized in boats, docks, and other marine equipment. - Electric & Electronics
Because of their high electrical conductivity, brass fasteners are widely employed in electrical and electronic applications. They are utilized in switches, circuit boards, and other electrical components that require reliable connections. - Auto Industry
Brass fasteners are utilized in electrical systems, engines, and other automotive components that need to be durable, corrosion resistant, and heat resistant. - Construction and Architecture.
Brass fasteners are also commonly employed in building and architecture, particularly in decorative applications. They can be found in luxury door handles, light fixtures, and decorative panels. - Plumbing:
Because of its resistance to corrosion, brass fasteners are widely used in plumbing, particularly in water supply systems, pipe fittings, and valves.
Challenges in Brass Fasteners Manufacturing
While brass fasteners offer several advantages, producers confront the following obstacles during the production process:
- Fluctuations in raw material prices might affect the cost of brass production. To achieve consistent output, manufacturers must remain agile while procuring raw materials.
- accuracy Requirements: Because industries like electronics and automobiles require high accuracy, manufacturers must invest in advanced machining processes to make fasteners with tight tolerances.
- Competition: The brass fasteners sector is fiercely competitive, with producers from all around fighting for market share. Companies must differentiate themselves via quality, innovation, and exceptional customer service.
Jamnagar: The Hub of Brass Fasteners Manufacturing
When it comes to brass fastener manufacturing, Jamnagar in Gujarat, India, is the global leader. Jamnagar, often known as the “Brass City,” is home to a number of small, medium, and large-scale brass product producers, including fasteners. The city’s strategic position, availability of trained workforce, and accessibility to raw material sources make it an ideal hub for brass production.
Jamnagar Brass Hub is a well-known manufacturer and supplier of high-quality brass fasteners.
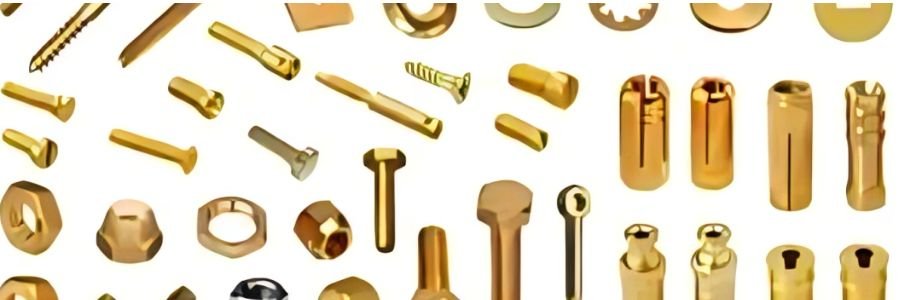
Jamnagar Brass Hub: Brass Fasteners Manufacturer
Jamnagar Brass Hub was founded with the objective of providing top quality brass fasteners and has swiftly established itself as a trusted name in the industry. With a commitment to excellence, innovation, and customer satisfaction, the company has been able to supply world-class fasteners to clients all over the world.
Key Features of Jamnagar Brass Hub
- Jamnagar Brass Hub’s manufacturing facility is state-of-the-art, with cutting-edge machinery and technology to assure precision and efficiency in brass fastener production.
- The company provides a wide selection of brass fasteners, such as screws, bolts, nuts, washers, rivets, and more. Jamnagar Brass Hub is the ideal fasteners for electrical applications, marine situations, and construction.
- Customization: Recognizing that diverse sectors have particular requirements, Jamnagar Brass Hub provides customized brass fasteners for specialized purposes. The company collaborates closely with customers to design and manufacture fasteners that match their specific needs.
- Quality Assurance: Quality is central to Jamnagar Brass Hub’s operations. The company employs stringent quality control techniques, from raw material sourcing to final product inspection, to ensure that every fastener satisfies worldwide standards.
- Sustainability: The company is dedicated to environmentally friendly manufacturing procedures, decreasing waste and energy consumption in its production operations. Brass is a recyclable material, and the Jamnagar Brass Hub takes steps to reduce its environmental impact.
- Global Reach: Jamnagar Brass Hub serves clients not only in India but also in international markets. The company’s fasteners are shipped to countries throughout the world, including the United States, the United Kingdom, the United Arab Emirates, and others.